Ginori 1735 has always been driven by a gracious yet daring spirit and natural creative flair. Since its founding, it has crafted an ideal of timeless, visionary beauty by designing and producing precious collections in hard porcelain, a ceramic material renowned for its resistance, translucency, and extra-fine quality. Combining the innate elegance of colors with a bold, contemporary touch, every creation narrates the brand’s historic manufacturing and artisanal excellence, embodying artistic Italian tradition and today’s innovative production technologies as one.
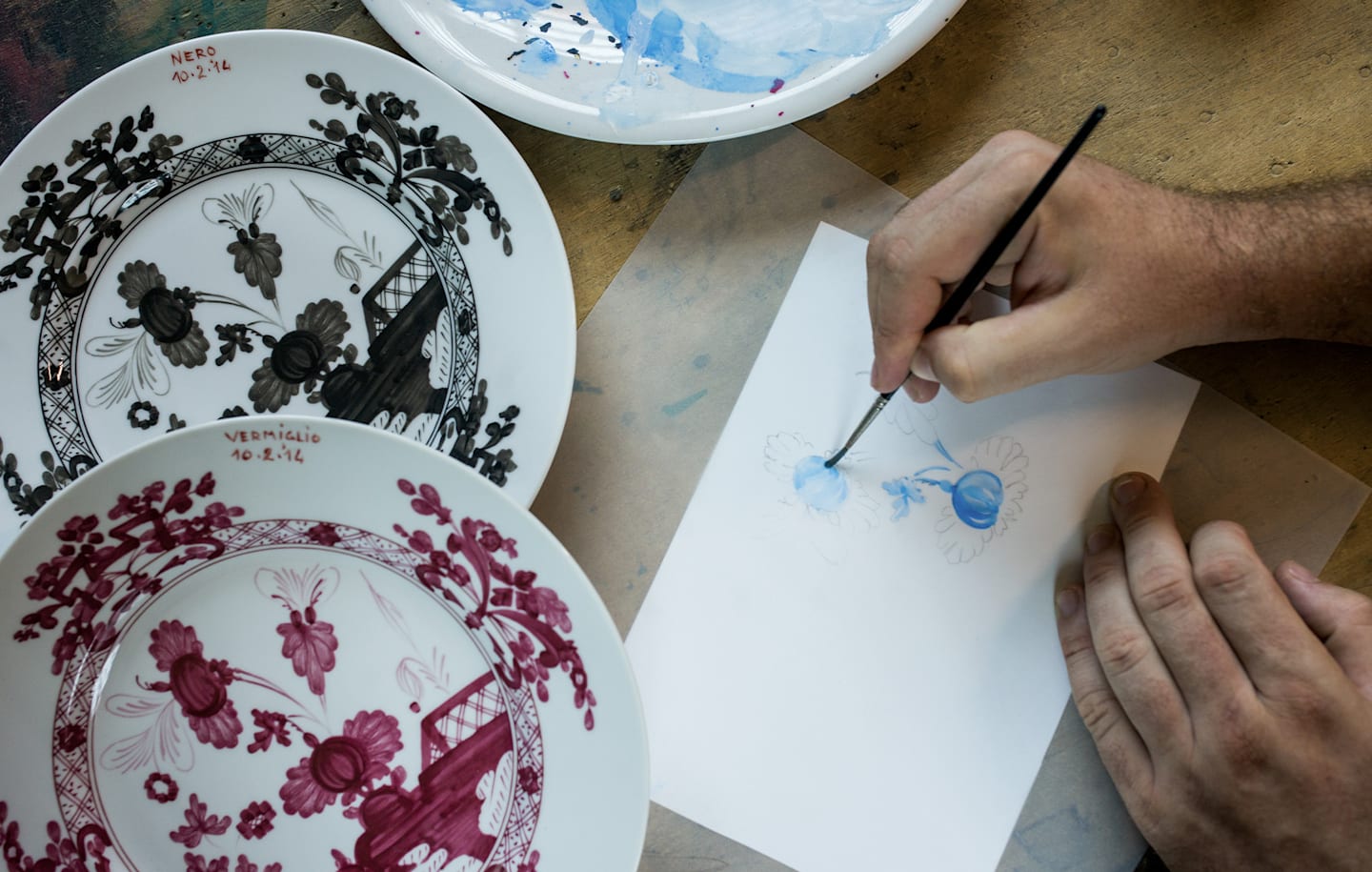
In the Design Department, our team of designers conceives and sketches the ideas and concepts for every Ginori 1735 collection.
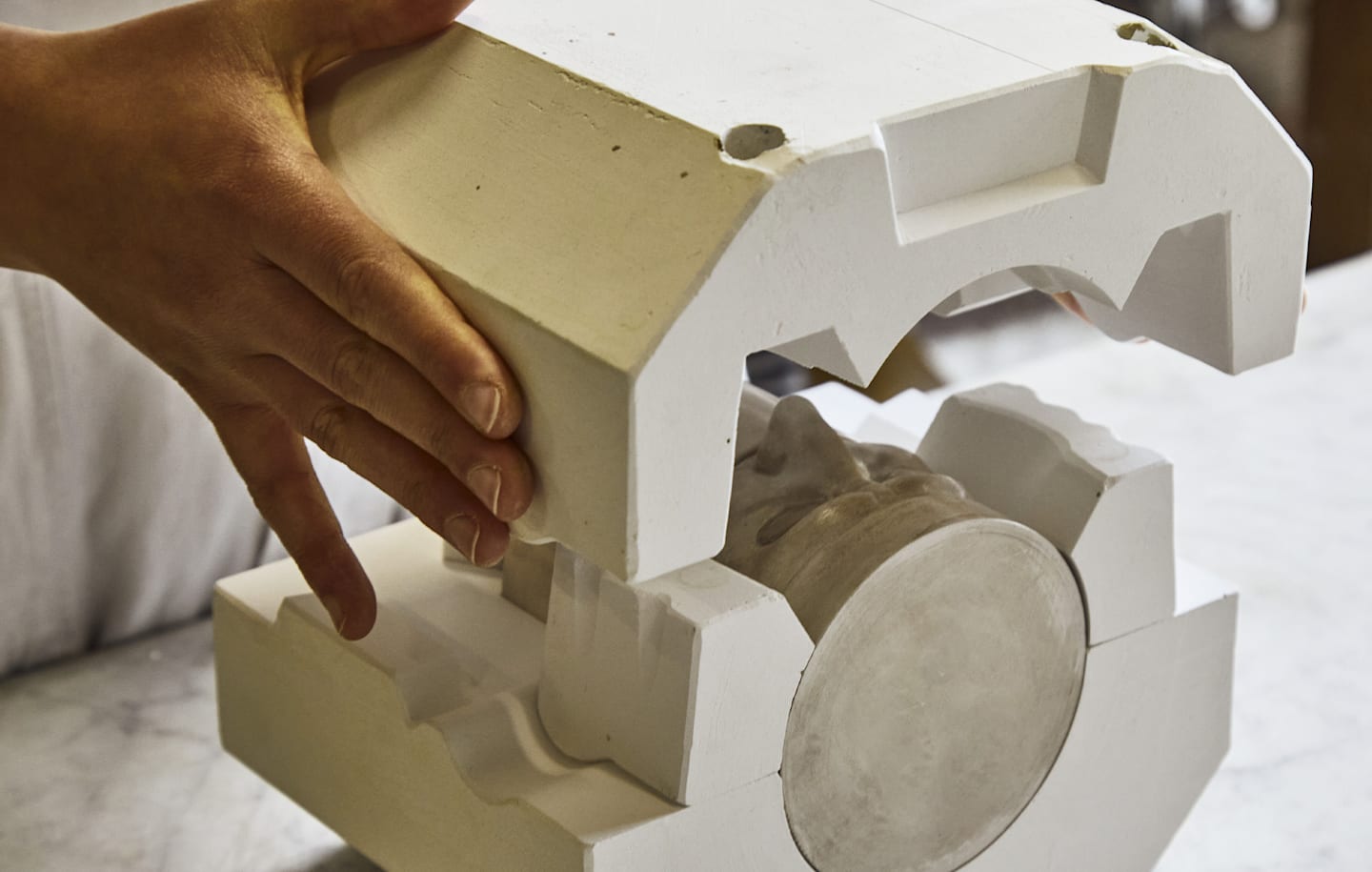
In the Modeling Department, our master sculptors craft the drawings to life, transforming each one into chalk molds for the production of our future porcelains.
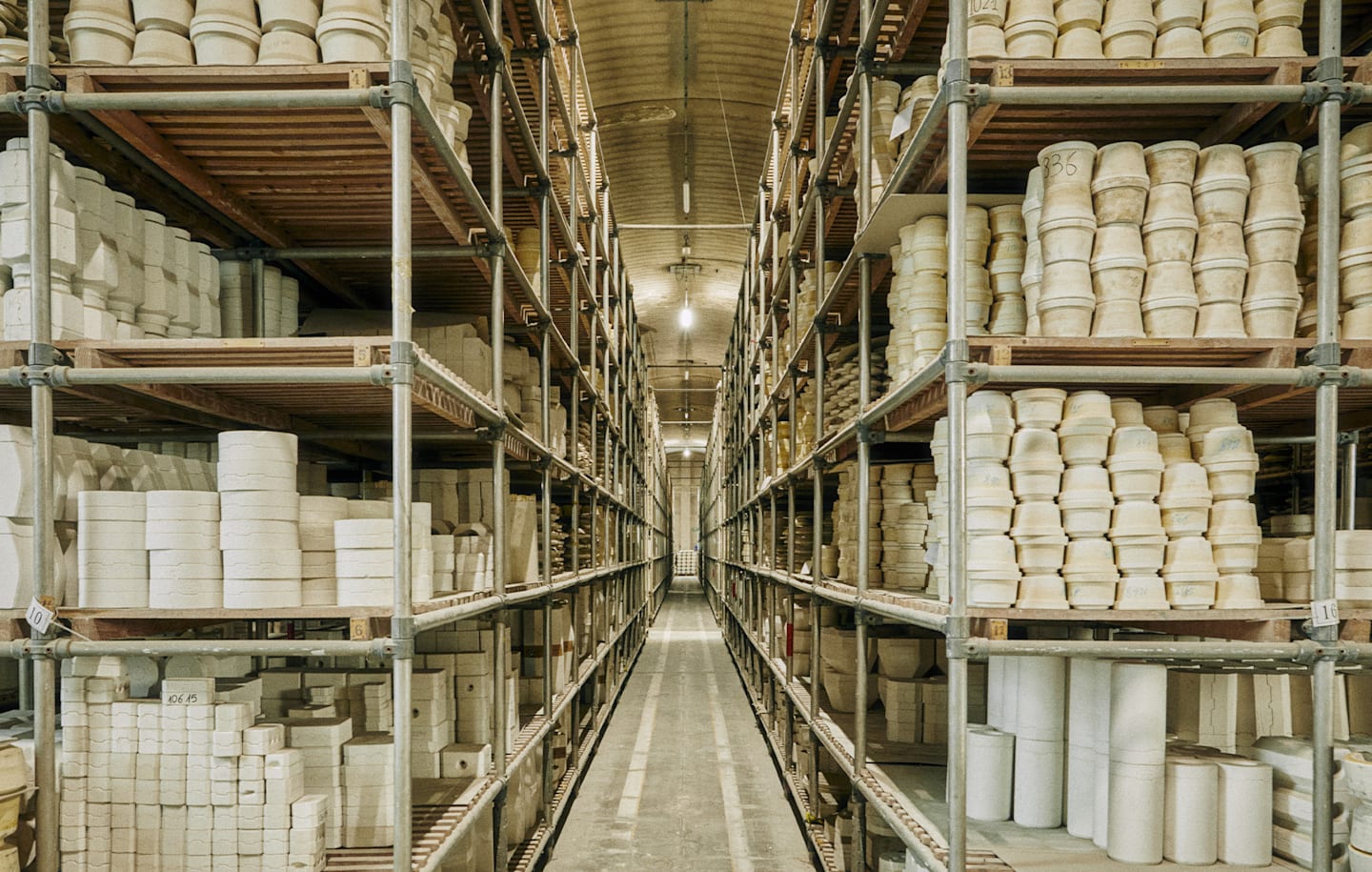
A truly magical space, the Voltone Archive is dedicated to preserving the original molds of every creation ever designed and produced at our Manifattura since 1735.
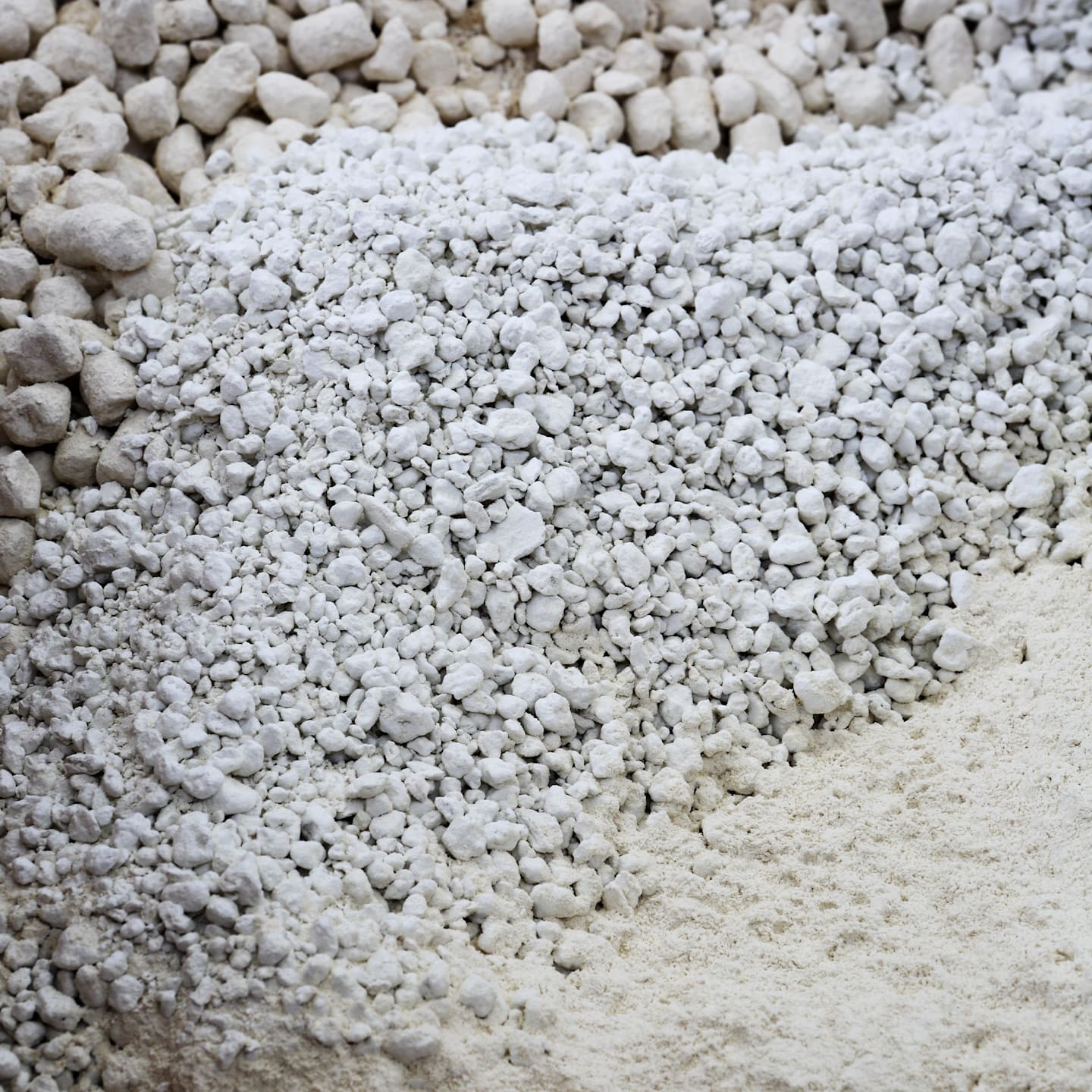
Ginori 1735 represents manufacturing mastery in hard porcelain production. This type of ceramic requires firing in two stages to achieve the hardness, translucency, and extra-fine quality it is sought for. It is made from a mixture of three fundamental components. The first is Kaolin (50%), a pure and natural white mineral clay used for plasticity, whiteness, and resistance. The second is Feldspar (25%), a group of minerals rich in metal aluminosilicates that helps the clay to melt, facilitating vitrification. Finally, Quartz (25%) enables the end product to be durable, compact, and non-porous.
At our Manifattura, we still make porcelain authentically, just like 300 years ago. From the molding and forming to the glazing, firing, and decoration, every step of production represents the human passion and meticulous attention to detail that have inspired Ginori 1735 since the beginning. Each creation can take 6-8 hours of craftsmanship, 5 different artisans, and more than 8 days to be completed. This process has always been, and still is, unique, distinguished today by the balance of traditional artisanal artistry and the ultra-advanced technologies required to deliver the highest quality porcelain.
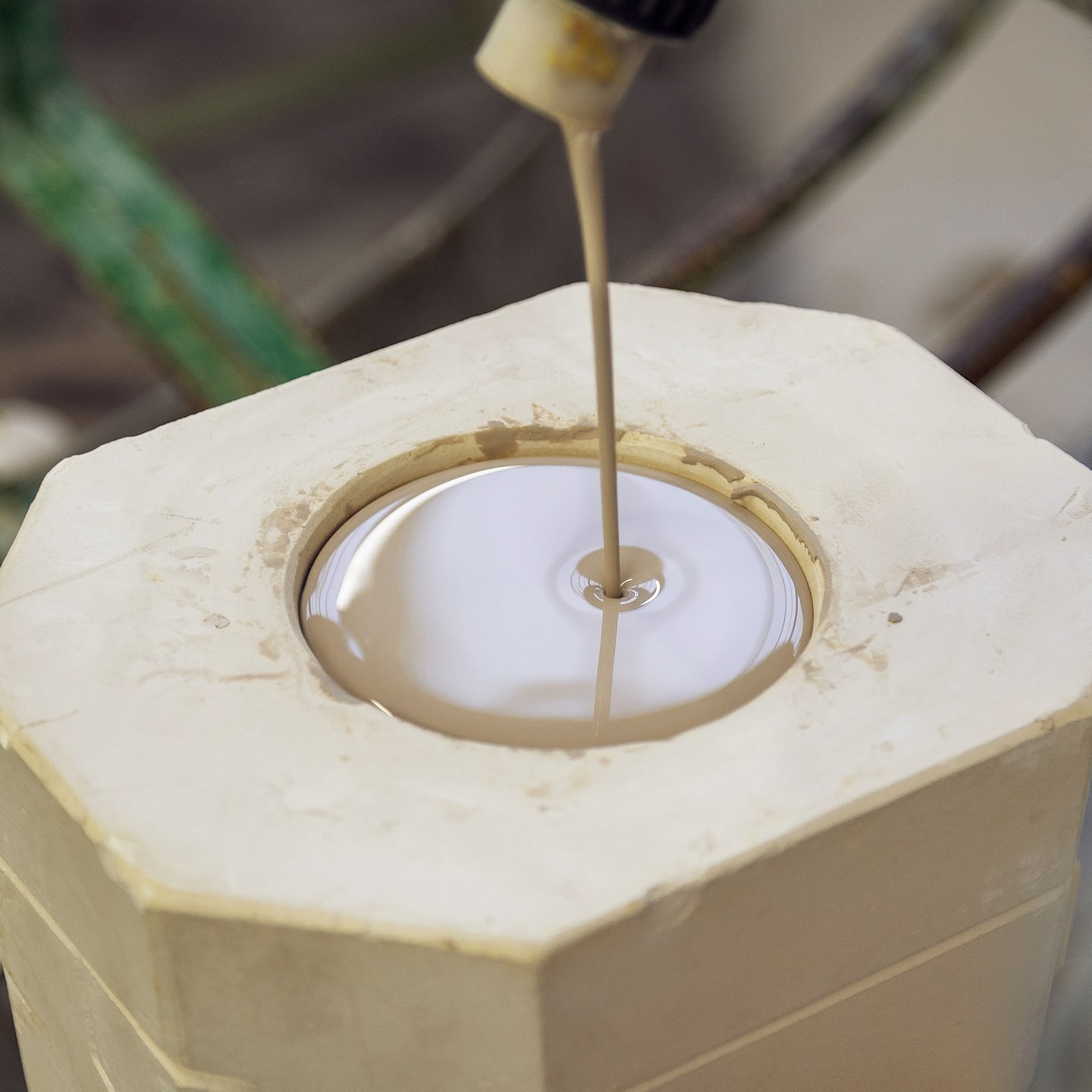
The plaster mold is a cube-like shape that contains the impression of our porcelain-to-be.Through the slip-casting technique, our artisans pour the mixture of kaolin, feldspar, and quartz into the mold, filling it. As the plaster’s porousness absorbs the mixture’s water, a solid layer of paste forms on the mold's inner walls, shaping our product. When ready, the mold can be opened to reveal the ‘crudo’—the raw piece—which is then garnished by hand with handles, knobs, spouts, and any other element it was designed with. Petite imperfections are refined using small blades and sponges to achieve aesthetic harmony and detail perfection.
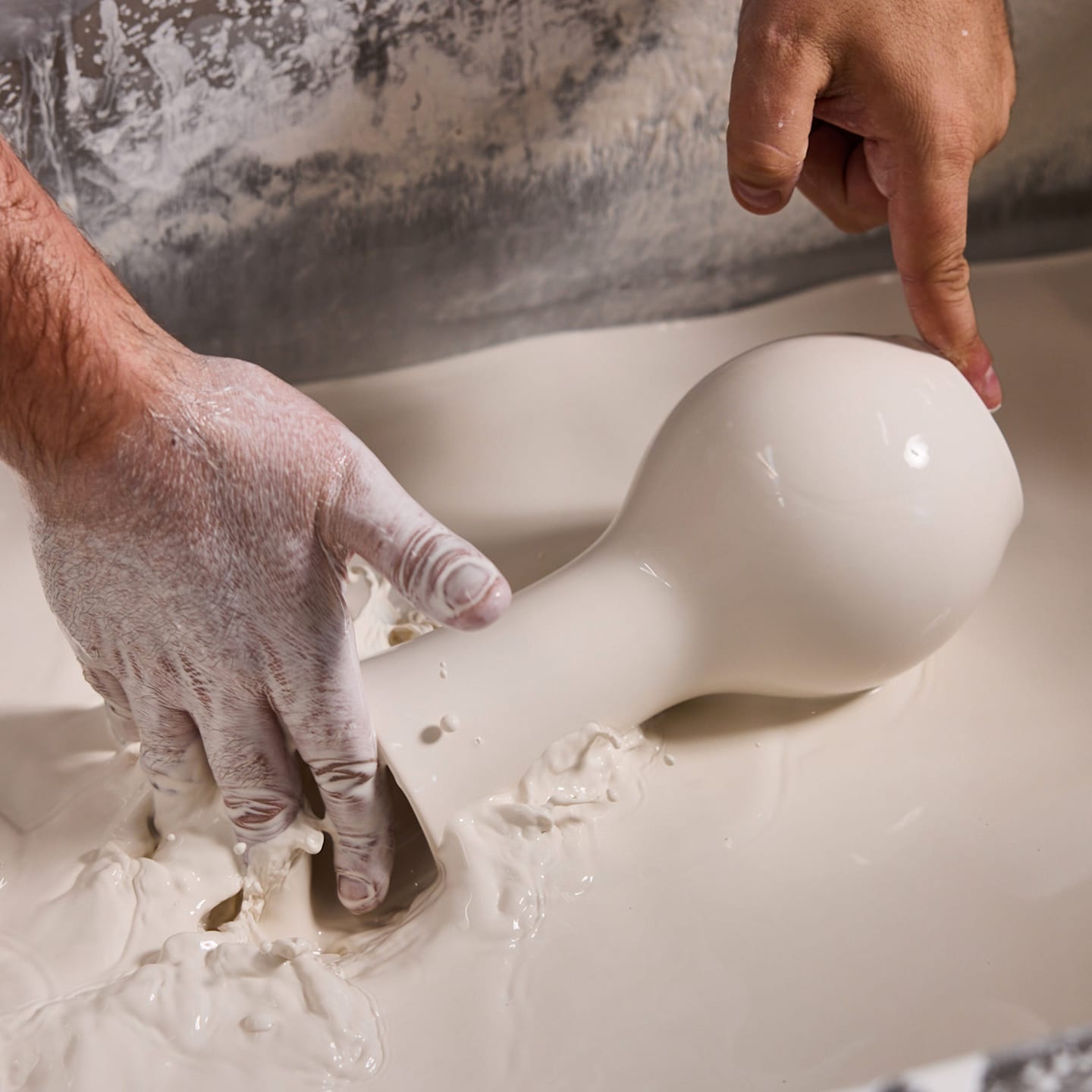
The raw product undergoes two firing stages. The first, bisque firing, is done at 1000°C to harden the clay body. Then, expert hands cover the piece with a uniform and smooth glaze by dipping the product in a mixture of pure water and quartz. The second, glaze firing, occurs at 1400°C through a delicate and technologically complex procedure to vitrify the porcelain. This allows the piece to lose its porosity and acquire hardness while developing a white, glossy, and translucent surface.
Beautifying an object makes it unique. During the production process, in which craftsmanship—the hallmark of Ginori 1735—and industrial passages converge, the creative ideas of our designers evolve into precious porcelains. In various phases, our artisanal spirit is enhanced through manual techniques such as decal application, gilding, airbrushing, and painting.
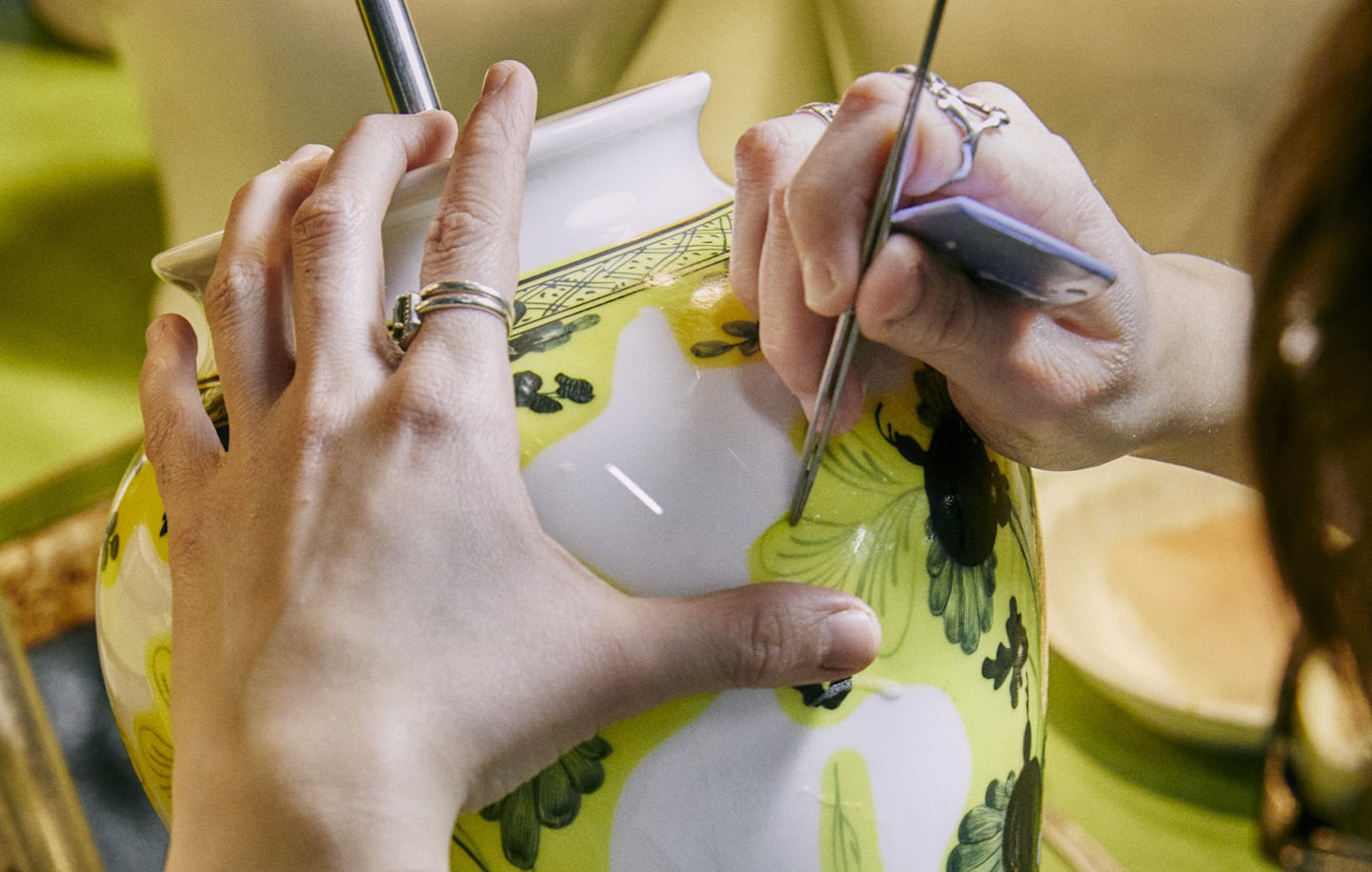
The porcelain’s allure is enhanced with decorative motifs and colorsthrough decals applied to its surface, carefully avoiding imperfections such as bubbles.
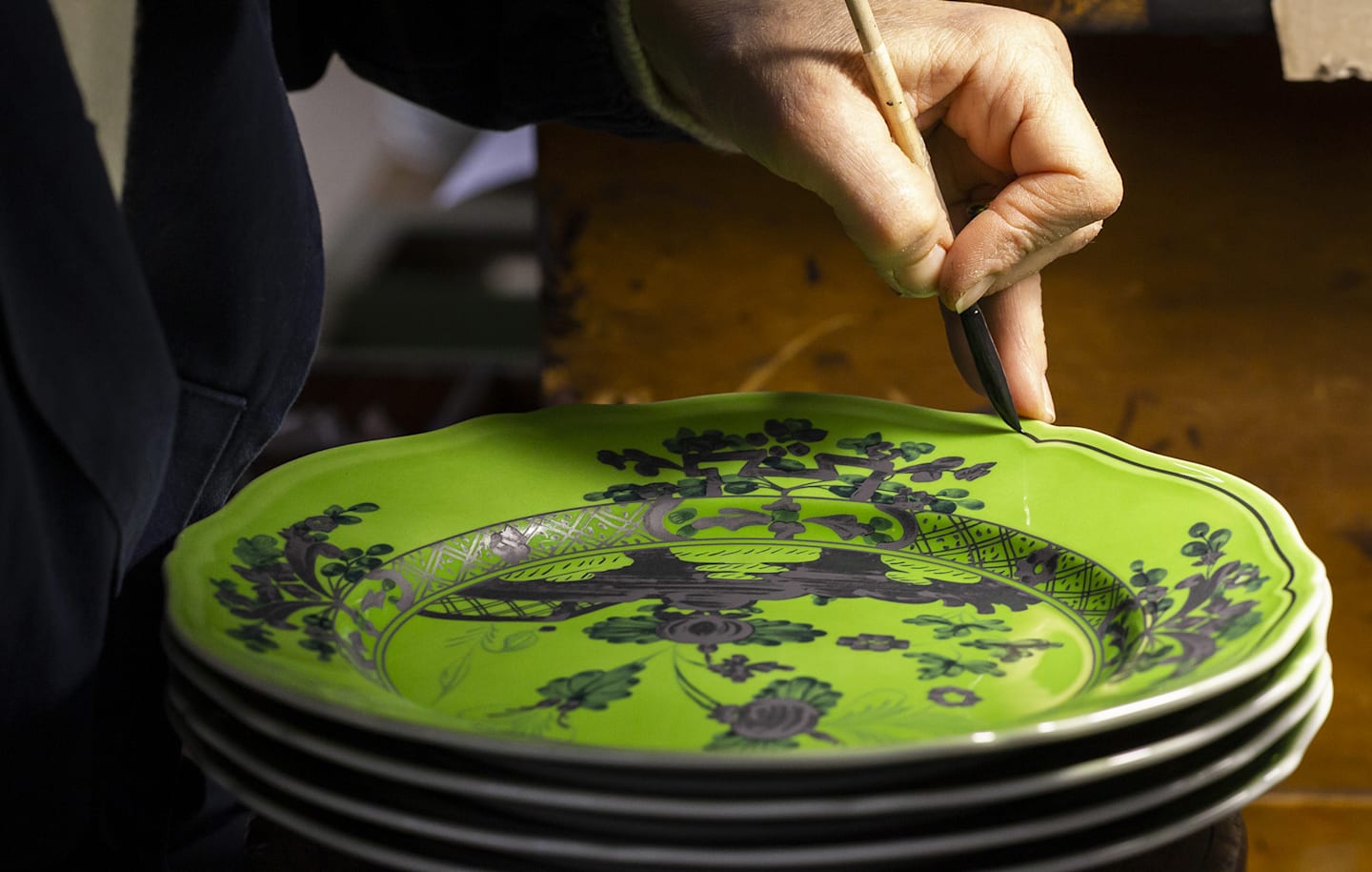
With a distinctive touch, Ginori 1735 outlines the silhouettes of its creations with charming colors and precious metals such as pure gold, bright gold, and platinum. High-demand collections are gilded using semi-automatic machinery.
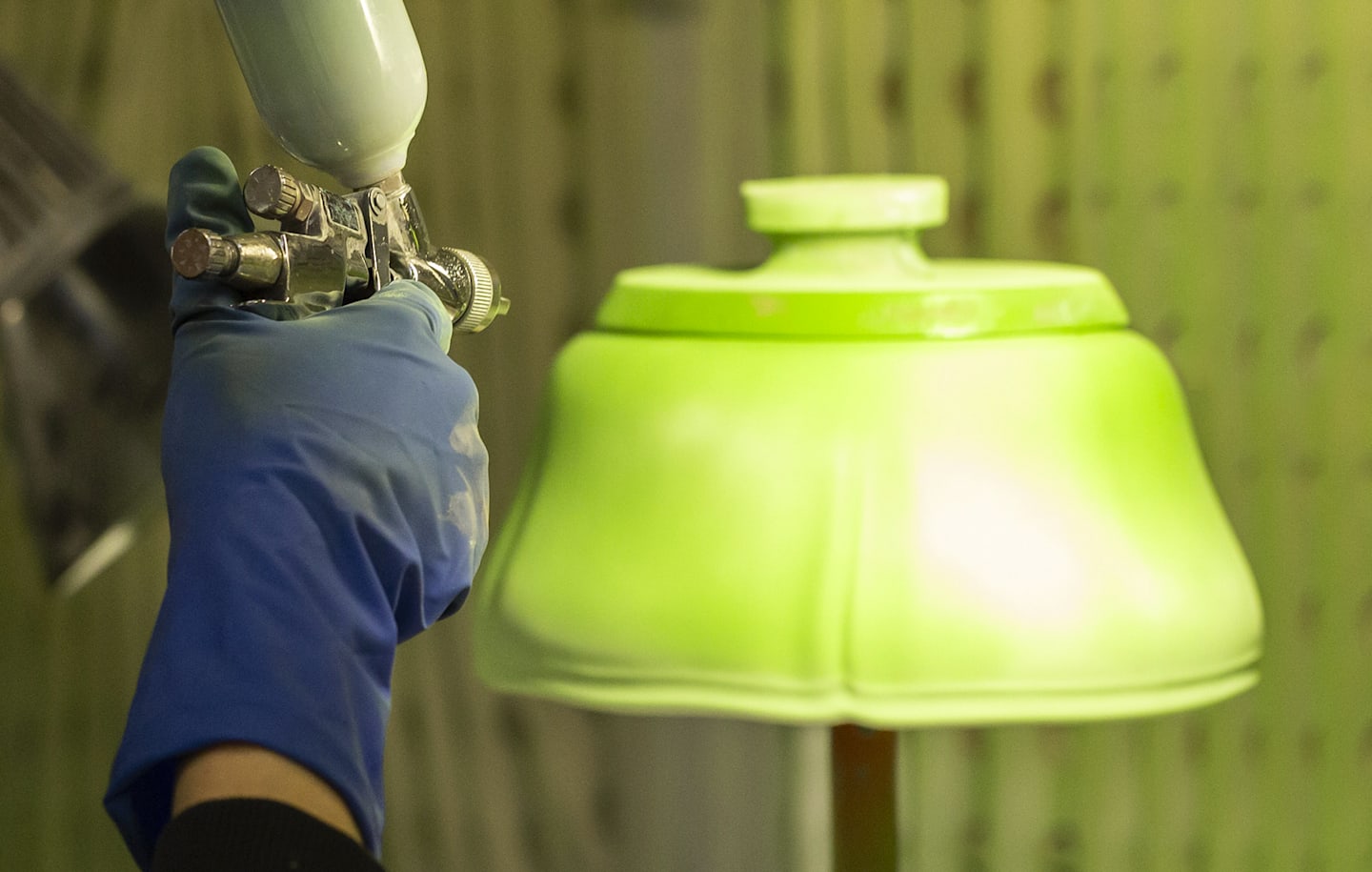
When airbrushing manually, obtaining the desired nuance in intensity and uniformity is a particularly demanding task. It requires our artisans to express their artistic sensitivity with patience, attending to every detail with minute precision.
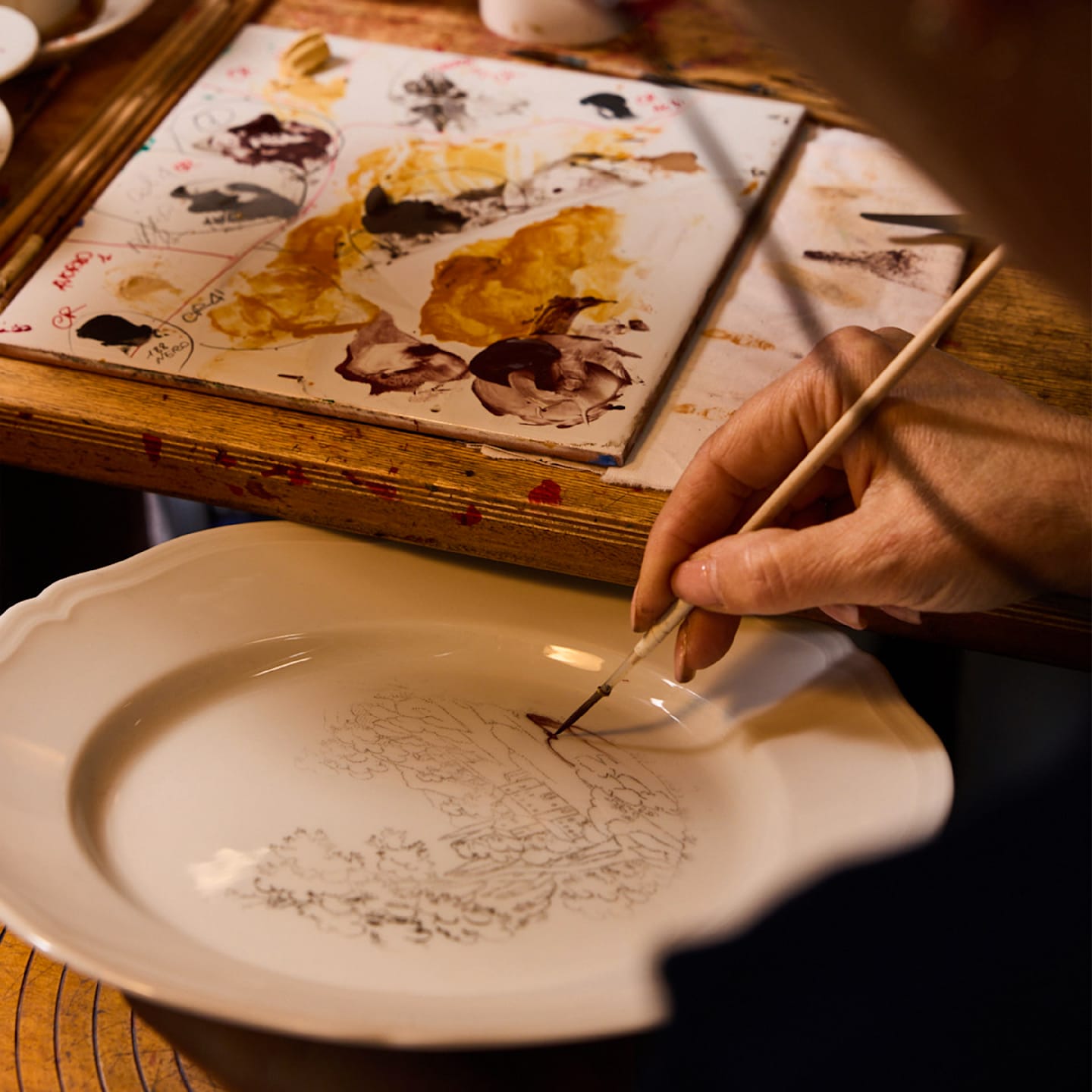
In our timeless painting workshop, where the air smells of the turpentine, a pine resin used to dilute powdery pigments and luxurious metals, the artists hand-paint the decorations of our most exclusive collections. Following the ‘Spolvero’ technique, a method applied in fresco painting to transfer a drawing onto a surface, every design comes to life through the magical natural touch of bristle brushes.
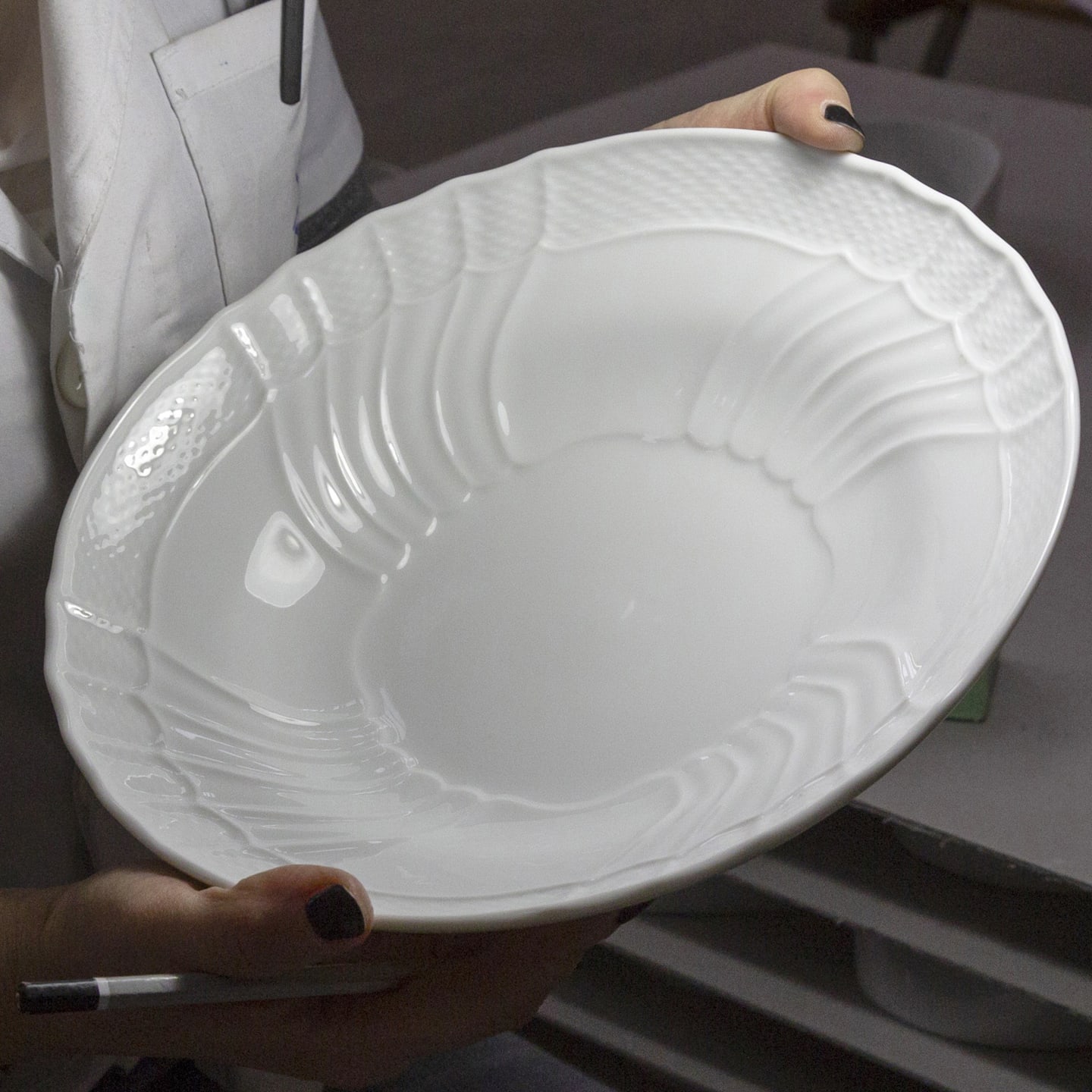
Quality is quintessential to the identity of our porcelains and production heritage. In the final stages, specialized personnel carefully examine each piece for defects; only the perfect ones progress to the finishing decoration phase.
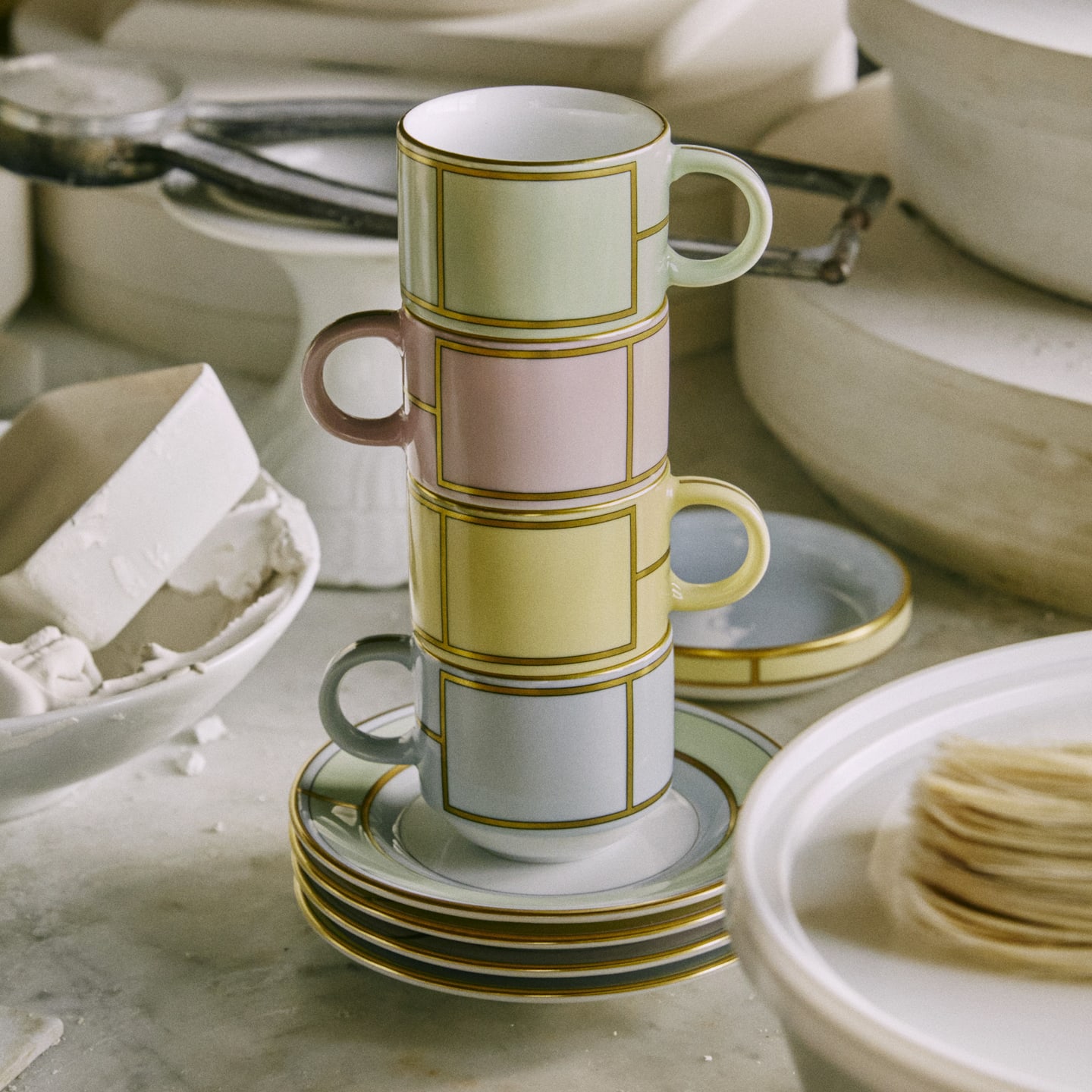
Today, Ginori 1735 continues to create hard porcelain collections honed by its long-standing heritage of manufacturing and artisanal know-how elevated by pure creativity. A one-of-a-kind touch that translates into tasteful table stories, synonymous with a refined and contemporary lifestyle inspired by audacious beauty and gracious elegance.